What is die casting
Die casting is a manufacturing process used to produce metal parts with high dimensional accuracy and surface finish. It involves forcing molten metal into a mold cavity under high pressure. The mold cavity is created by two hardened steel dies that are machined into the desired shape.
The process starts with the melting of the metal, typically aluminum, zinc, or magnesium, in a furnace. The molten metal is then injected into the mold at high pressure using a hydraulic press. The metal solidifies quickly inside the mold, and the two halves of the mold are opened to release the finished part.
Die casting is widely used to produce parts with complex shapes and thin walls, such as engine blocks, transmission housings, and various automotive and aerospace components. The process is also popular in the production of consumer goods, such as toys, kitchenware, and electronics.
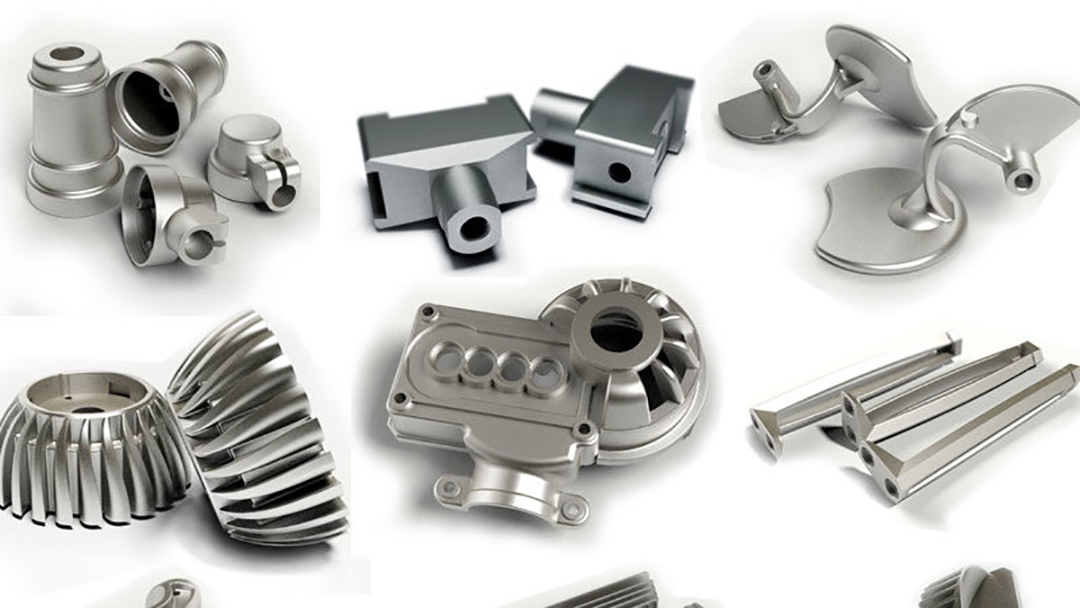
Pressure Die Casting
Die casting is a fairly specialised process which has developed more predominantly within the 20th century. The basic process comprises of: molten metal is poured/injected into a steel mould and via high velocity, constant and intensifying pressure (in pressure die casting) and cooling the molten metal solidifies to form a solid casting. Typically, the process itself only takes a few seconds and is a quick way of forming metal product from raw material. Die casting is suited to materials such as tin, lead, zinc, aluminium, magnesium to copper alloys and even iron alloys such as stainless steel. The main alloys utilised today in pressure die casting are aluminium, zinc and magnesium. From the early die cast machines which orientated die tools in vertical orientation to the now common standard of horizontal orientation and operation, four tie bar tensioning and fully computer controlled process stages the process has advanced throughout the years.
The industry has grown into a worldwide manufacturing machine, making components for a variety of applications, many of which will be in reach from ones self as the product application of die castings is so diverse.
Benefits of pressure die casting
Some of the benefits of high pressure die casting:
• The process is suited to high volume production.
• Produce fairly complex castings quickly compared to other metal forming processes (eg. machining).
• High strength components produced in the as cast condition (subject to component design).
• Dimensional repeatability.
• Thin wall sections possible (eg. 1-2.5mm).
• Good linear tolerance (eg. 2mm/m).
• Good surface finish (eg. 0.5-3 µm).
Because of this “closed” metal melt/injection system and minimal mechanical movement hot chamber die casting can provide better economies for production. Zinc metal alloy is primarily used in hot chamber pressure die casting which has a fairly low melting point which offers further benefits for low wear on machines (pot, gooseneck, sleeve, plunger, nozzle) and also low wear on die tools (so longer tool life compared to aluminium die casting tools – subject to casting quality acceptance).
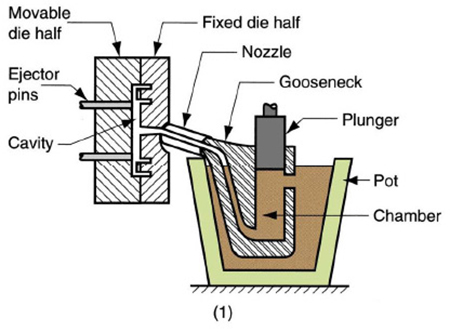
Cold chamber machines are suited for aluminium die casting, parts on the machine (shot sleeve, plunger tip) can be replaced over time, sleeves can be metal treated to increase their durability. Aluminium alloy is melted in a ceramic crucible due to aluminium’s relative high melting point and the need to reduce the risk of iron pickup which is a risk within ferrous crucibles. Because aluminium is a relatively light metal alloy it affords casting of large and heavy die castings or where increased strength and lightness in die castings is required.
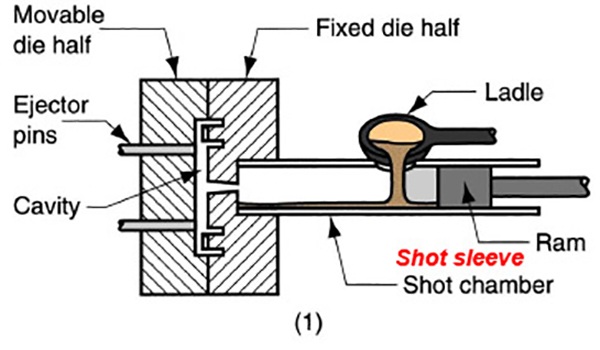