1. Laser Marking
Laser marking is a common method of permanently marking CNC machining components with high precision and accuracy. The process involves using a laser to etch a permanent mark onto the surface of the part.
The laser marking process begins by designing the mark to be placed on the part using CAD software. The CNC machine then uses this design to direct the laser beam to the precise location on the part. The laser beam then heats the surface of the part, causing a reaction that results in a permanent mark.
Laser marking is a non-contact process, meaning there is no physical contact between the laser and the part. This makes it suitable for marking delicate or fragile parts without causing damage. Additionally, laser marking is highly customizable, allowing for a wide range of fonts, sizes, and designs to be used for the mark.
The benefits of laser marking in CNC machining parts include high precision and accuracy, permanent marking, and non-contact process that minimizes damage to delicate parts. It is commonly used in the automotive, aerospace, medical, and electronic industries to mark parts with serial numbers, logos, barcodes, and other identification marks.
Overall, laser marking is a highly effective and efficient method of marking CNC machining parts with precision, accuracy, and permanence.
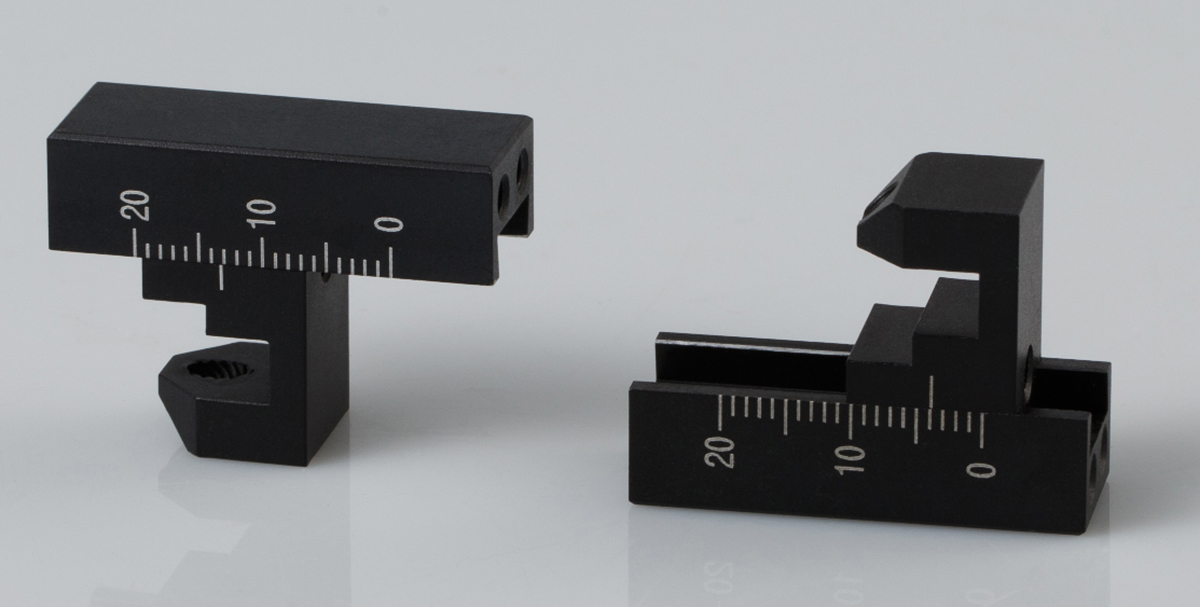
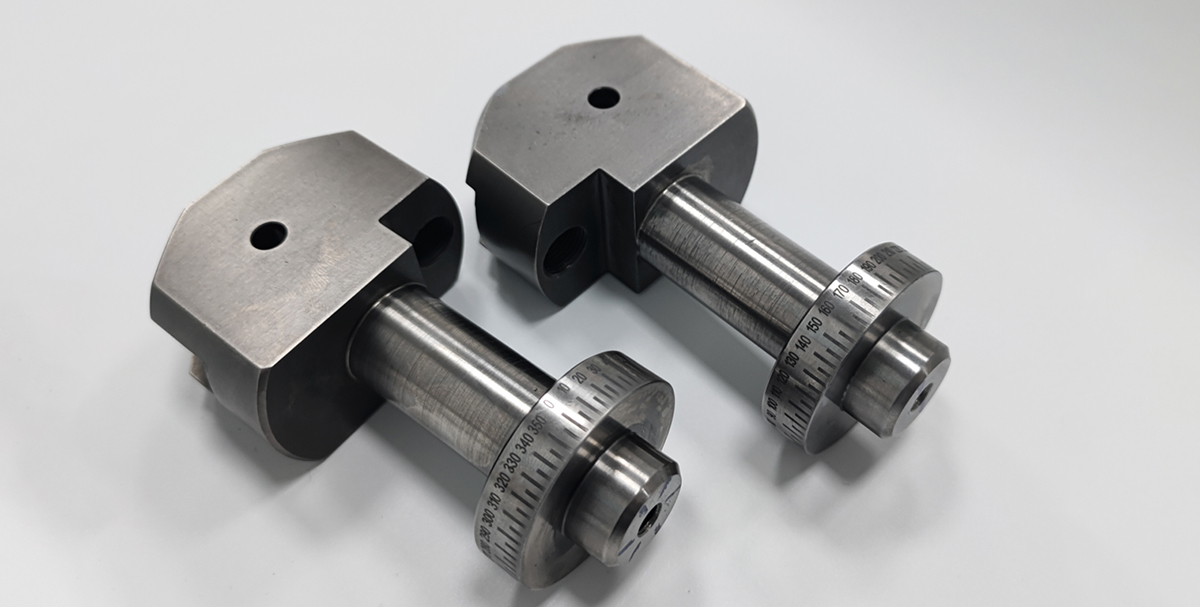
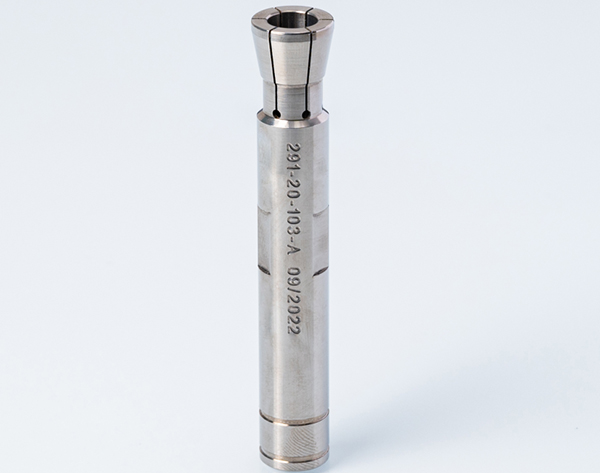
2. CNC Engraving
Engraving is a common process used in CNC machine part to create permanent, high-precision marks on the surface of parts. The process involves using a tool, typically a rotating carbide bit or diamond tool, to remove material from the surface of the part to create the desired engraving.
Engraving can be used to create a wide variety of marks on parts, including text, logos, serial numbers, and decorative patterns. The process can be performed on a wide range of materials, including metals, plastics, ceramics, and composites.
The engraving process starts with designing the desired mark using CAD software. The CNC machine is then programmed to direct the tool to the precise location on the part where the mark is to be created. The tool is then lowered onto the surface of the part and rotated at high speeds while it removes material to create the mark.
Engraving can be performed using different techniques, including line engraving, dot engraving, and 3D engraving. Line engraving involves creating a continuous line on the surface of the part, while dot engraving involves creating a series of closely spaced dots to form the desired mark. 3D engraving involves using the tool to remove material at different depths to create a three-dimensional relief on the surface of the part.
The benefits of engraving in CNC machining parts include high precision and accuracy, permanent marking, and the ability to create a wide range of marks on a variety of materials. Engraving is commonly used in the automotive, aerospace, medical, and electronic industries to create permanent marks on parts for identification and tracking purposes.
Overall, engraving is an efficient and precise process that can create high-quality marks on CNC machining parts.
3. EDM marking
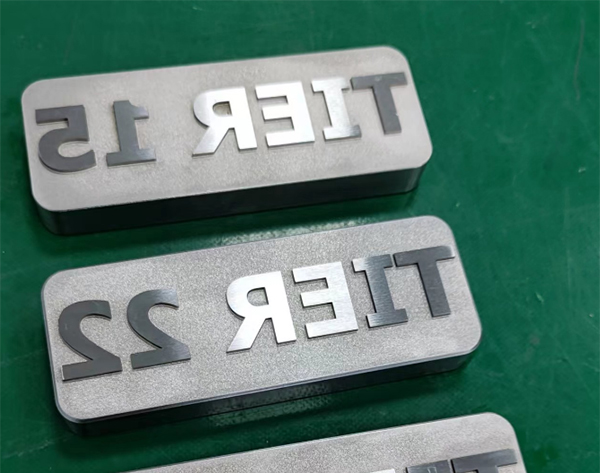
EDM (Electrical Discharge Machining) marking is a process used to create permanent marks on CNC machined components. The process involves using an EDM machine to create a controlled spark discharge between an electrode and the surface of the component, which removes material and creates the desired mark.
The EDM marking process is highly precise and can create very fine, detailed marks on the surface of components. It can be used on a wide range of materials, including metals such as steel, stainless steel, and aluminum, as well as other materials like ceramics and graphite.
The EDM marking process starts with designing the desired mark using CAD software. The EDM machine is then programmed to direct the electrode to the precise location on the component where the mark is to be created. The electrode is then lowered onto the surface of the component, and an electrical discharge is created between the electrode and the component, removing material and creating the mark.
EDM marking has several benefits in CNC machining, including its ability to create highly precise and detailed marks, its ability to mark hard or difficult-to-machine materials, and its ability to create marks on curved or irregular surfaces. Additionally, the process does not involve physical contact with the component, which minimizes the risk of damage.
EDM marking is commonly used in the aerospace, automotive, and medical industries to mark components with identification numbers, serial numbers, and other information. Overall, EDM marking is an effective and precise method for creating permanent marks on CNC machined components.